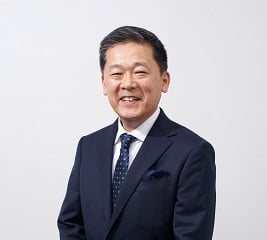
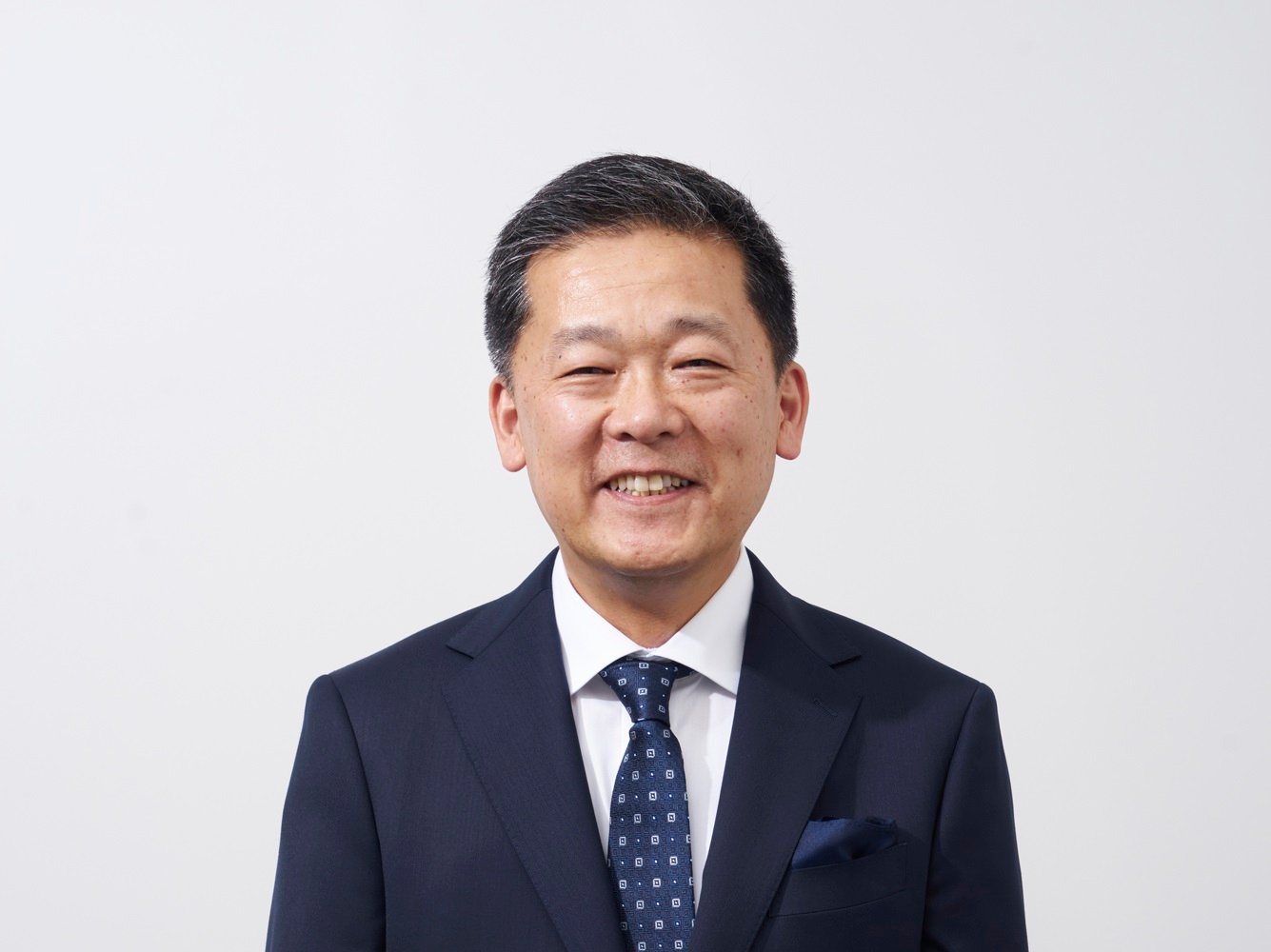
Facilitating daily management of made-to-order through DX to realize high-mix, low volume, and prompt delivery
BPR leader:
Keizo Yamaguchi
Chief Manufacturing Officer (CMFO)
■ DX realizing time-based competition at production sites
i-PRO has factories at two sites, in Suzhou and Fukuoka, where a workforce of approximately 500 employees are engaged in production. For us at the production sites, the transformation to realize our strategy of time-based competition, which aims to realize maximization of value provided to customers, is not simply improvement to production management and production technology, it involves fundamental changes to our values until now.
Prior to our company becoming independent, production was in accordance with plans drawn up in monthly cycles based on forecast demand from our group’s sales company (confirmed three-months in advance). These forecasts confirmed in three-month blocks had a high risk of deviating from actual achievements, resulting in us holding product inventory, making it difficult to respond to our customers’ urgent projects, and causing lost sales opportunities.
Since i-PRO became independent, we aim to achieve high-mix, low volume, and prompt delivery through time-based competition. For this, we must achieve daily made-to-order production, which requires us to reform site management, including production processes, while simultaneously transforming product design (modular design). Our independence provides opportunities for self-sufficient systems, and to globally integrate key systems, accelerating transformation. The monthly task of preparing the production plan from the demand forecast, enabled by people’s experience, can now be implemented daily through the power of digital, and we can also closely examine improvements to production technology to achieve our daily plan. As a result, we cut our global inventory by 50% in two years and also dramatically reduced the number of missed opportunities. We can also now aim to cut production costs to one-third of conventional levels.
■ Introducing global production standard configurations to achieve further growth
Due to accelerating developments, we are currently redefining production processes and advancing the introduction of new factory systems to support them. Our new process system, known as the i-PRO Manufacturing Digital Platform System (MDP) is our new global production standard, which we will apply as we increase production sites, enabling us to launch new sites in less time. Also, introduction of MDP has linked all processes through data is expected to boost traceability, further enhance product quality, and achieve greater work efficiency. All members are tackling reform as part of these initiatives by production sites, so that they directly contribute to provision of value to customers.